In the field of mold manufacturing, the design of mold heating tubes is crucial. Its shape and size must closely fit the complex structure of the mold in order to achieve efficient and uniform heating.
1、 Analysis of complex die structure
Firstly, it is necessary to conduct a detailed analysis of the shape of the mold. If the mold is a simple flat shape, a straight heating tube may be sufficient to meet the heating requirements. But if the mold has complex cavities, such as those with deep holes, narrow grooves, or irregular surfaces, special design is required. For example, for molds with deep holes, the heating tube can be designed as a slender rod to heat deeply into the hole, ensuring uniform temperature throughout the entire hole wall.
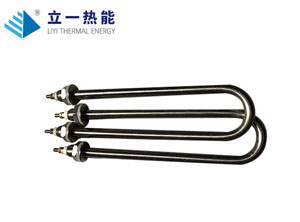
For molds with curved surfaces, curved heating tubes can better fit the surface. Through computer-aided design (CAD) software, the distribution of heating tubes along the curved surface can be accurately simulated, ensuring that the distance between the heating tube and the mold surface is as consistent as possible, thus ensuring the uniformity of heating.
2、 Key points of shape design
When designing the shape of the heating tube, the bending radius of the heating tube should be considered. If the bending radius is too small, it may cause the heating wire inside the heating tube to be compressed, affecting its service life and even causing safety hazards such as short circuits. Generally speaking, the bending radius should be greater than 3-5 times the diameter of the heating tube.
In addition, for some complex molds with multiple independent heating zones, the heating tube can be designed in segmented form. For example, in injection molds, different cavities may require different temperatures. In this case, the heating tube can be divided into several independent parts, and each part controls the temperature of a cavity, thus achieving precise heating of different areas.
3、 Key points of size design
The size of the heating tube mainly includes length and diameter. The length design should be determined based on the size of the heating area of the mold. If the heating area is large, a longer heating tube is needed to cover the entire area. At the same time, the power distribution of the heating tube should be considered to avoid the end temperature being too low due to its long length.
The diameter of the heating tube should take into account both the heating power and the spatial limitations of the mold. Larger diameter heating tubes can provide higher power, but may occupy more internal space in the mold. In molds with limited space, it is necessary to choose smaller diameter heating tubes and meet the heating requirements by increasing the number of heating tubes or adjusting the power.
In short, the design of the shape and size of the mold heating tube is a complex process that requires full consideration of various factors such as the complex structure of the mold, heating requirements, heating uniformity, and space limitations. Only in this way can suitable heating tubes be designed to provide efficient and stable heating services for molds.