The installation position of the mold heating tube in the mold is crucial, as it directly affects the heating effect, molding quality, and service life of the mold.
Firstly, for simple molds with regular shapes, such as cube or rectangular molds, heating tubes are usually installed in a uniformly distributed manner. Symmetrically arranging heating tubes on the side, bottom, and other positions of the mold can ensure that heat is evenly transferred to all parts of the mold. For example, around the rectangular cavity of an injection mold, heating tubes are installed equidistant on the outside of the cavity wall to ensure a uniform temperature environment for the plastic melt in the cavity, avoiding defects such as shrinkage marks and warping caused by local overheating or undercooling.
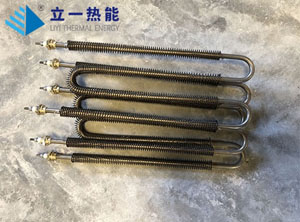
If the mold has a complex internal structure, such as deep holes, blind holes, or complex core structures, the installation of the heating tube needs to consider these special parts. For deep or blind holes, small heating tubes can be inserted into the holes to ensure that these areas receive sufficient heat. In a mold with a core, the heating tube should be installed around the core to ensure that the core temperature is consistent with the cavity temperature. This way, during the molding process, the cooling rate of each part of the plastic product is similar, which is beneficial for ensuring the dimensional accuracy of the product.
For large molds, it may be necessary to install heating tubes in different zones. Due to the difficulty of heating large molds as a whole, dividing the mold into multiple heating zones, installing independent heating tube groups in each zone, and equipping them with corresponding temperature sensors and controllers can more accurately control the temperature in different zones. For example, in a large die-casting mold, according to the different wall thickness and shape characteristics of the castings, the mold is divided into multiple heating zones such as near the gate, thick wall area, and thin wall area, and heating tubes are installed separately to achieve differential temperature control in different areas and effectively improve the quality of the castings.
In addition, the installation position of the heating tube should also avoid interference with the moving parts of the mold. In molds with movable parts such as sliders and ejector pins, the heating tube should be installed in a position that does not affect the movement of these parts, to prevent damage to the heating tube during mold opening and closing or product ejection. At the same time, it is also necessary to consider whether the installation position of the heating tube is convenient for later maintenance and replacement, and reserve sufficient space for operators to carry out maintenance and other operations.