The insulation performance of the mold heating tube is crucial, as it directly affects the safety and stability of the equipment.
1、 Insulation resistance standard
At room temperature, the insulation resistance of the mold heating tube is generally required to be no less than 100M Ω (megaohms). Insulation resistance is a fundamental indicator for measuring the insulation performance of dielectric materials. This high resistance value can effectively prevent current leakage, ensuring that the heating tube can flow along the expected conductor (heating wire) under normal operating voltage, without leaking to the surrounding environment or mold through the insulation layer. When the insulation resistance is too low, leakage may occur, which increases the risk of electric shock for operators and also affects the normal working efficiency of the heating tube.
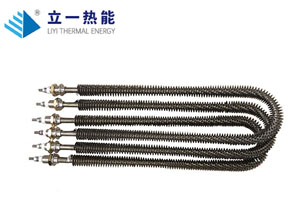
2、 Standard for compressive strength
The withstand voltage strength is also a key indicator for evaluating the insulation performance of mold heating tubes. Usually, the mold heating tube needs to be able to withstand a certain high voltage without being broken down. For example, for a mold heating tube with a rated voltage of 220V, its withstand voltage test voltage generally needs to reach around 1500-2000V. This is to ensure that in practical use, even in the event of momentary voltage fluctuations, the insulation layer of the heating tube can withstand additional voltage shocks and prevent insulation damage. If the withstand voltage strength is insufficient, when encountering peak voltage or other electromagnetic interference in the power grid that causes abnormal voltage rise, the insulation layer may be broken down, leading to short circuit faults.
3、 Performance requirements for insulation materials
There are also strict standards for the insulation material of mold heating tubes. Common insulation materials include magnesium oxide powder, etc. These materials require high dielectric constant, low dielectric loss, and good thermal stability. A high dielectric constant can ensure effective isolation of current under the action of an electric field; Low dielectric loss can reduce the loss of electrical energy in insulation materials and convert it into heat, avoiding local overheating; Good thermal stability enables insulation materials to maintain their insulation performance even in high-temperature environments during heating tube operation, without experiencing insulation performance degradation or decomposition due to temperature rise.
4、 Environmental adaptability standards
The insulation performance of the mold heating tube also needs to consider its stability in different environments. For example, in a humid environment, moisture may infiltrate the insulation layer, reducing insulation resistance. So it is required that the insulation layer of the heating tube has a certain degree of moisture resistance. At the same time, in environments with corrosive gases or chemicals, insulation materials cannot undergo chemical reactions with these substances to ensure their insulation performance is not corroded.
In order to ensure that the mold heating tube meets the insulation performance standards, strict quality testing is required during the production process, including insulation resistance testing, withstand voltage testing, etc. It is also necessary to regularly check its insulation performance during use to ensure the safe and reliable operation of the equipment.