When selecting the power of the mold heating tube, the size of the mold and the required heating rate are two key factors.
Firstly, consider the size of the mold. Larger molds require higher power to achieve effective heating. This is because the larger the volume of the mold, the greater its heat capacity. For example, a small injection mold may have a size of only a few tens of centimeters square and a relatively small heat capacity. Assuming the volume of this small mold is 10 cubic decimeters and the material is ordinary steel, its heat capacity is approximately 460 kJ/℃ (the specific heat capacity of steel is about 0.46 kJ/(kg ·℃), and the density is about 7.8 kg/dm ³). A large die-casting mold, with a volume of several cubic meters, can increase its heat capacity by hundreds or thousands of times.
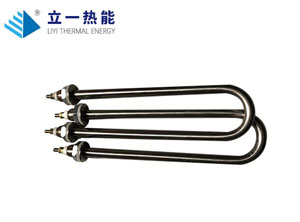
For the required heating rate, the faster the heating, the higher the required power. If you want to raise the mold temperature to the set value in a short period of time, a large power input is required. For example, if a mold is required to heat up from 20 ℃ to 200 ℃ within 10 minutes, compared to completing the same heating process within 30 minutes, the former requires much more power. Taking a mold with a heat capacity of 1000kJ/℃ as an example, to raise the temperature by 180 ℃ within 10 minutes (600 seconds), the required power is approximately 30kW according to the heat calculation formula Q=mc Δ T (Q is heat, m is mass, c is specific heat capacity, Δ T is temperature change) and the power calculation formula P=Q/t (P is power, t is time); If the time is extended to 30 minutes (1800 seconds), the required power is about 10kW.
At the same time, the material and initial temperature of the mold also need to be considered. The thermal conductivity of different materials varies. For example, copper molds have good thermal conductivity, high heating efficiency, and may require relatively less power; Ceramic molds have poor thermal conductivity, which may require higher power to achieve the same heating effect. In addition, when the initial temperature of the mold is low, more heat is required to heat it to the set temperature, and the power should be correspondingly increased.
In addition, the layout of the heating tube will also affect the power selection. A reasonable layout can make the heat distribution more uniform and reduce the occurrence of local overheating or insufficient heating. If the distribution of heating tubes is sparse, higher power may be required to compensate for the problem of uneven heat transfer; A tight and reasonable layout can achieve better heating effects at relatively low power. In practical selection, one can refer to the recommendations of the mold manufacturer, previous heating experience of similar molds, or estimate the appropriate heating tube power through simulation software.