In the large-scale production of 3D hot bending glass, the heating tube serves as a key heating element, and the balance between energy consumption and production efficiency directly affects the economic benefits and market competitiveness of the enterprise. To achieve an optimized balance between the two, efforts can be made from the following aspects.
1、 Equipment selection and upgrade
The selection of effective energy-saving heating tubes is the foundation. The new heating tube adopts cutting-edge materials and manufacturing processes, which can improve heating efficiency and reduce energy consumption. For example, some heating tubes that use special alloy heating wires can generate heat faster and reduce heat loss at the same power, allowing the glass to reach the required temperature for hot bending faster and shortening the production cycle. At the same time, regular testing and maintenance of heating tubes should be carried out, and aging and performance declining heating tubes should be replaced in a timely manner to ensure that the equipment is always in the best operating condition, avoiding production stagnation and additional energy consumption caused by equipment failures.
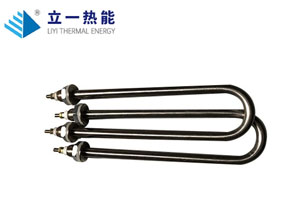
2、 Process optimization
Accurately controlling the parameters of the hot bending process is crucial. Determine the optimal heating temperature, time, and heating rate for different specifications of 3D hot bending glass through experiments and data analysis. For example, for thinner glass, appropriately reducing the heating temperature and accelerating the heating rate can ensure the quality of hot bending while reducing energy consumption. Adopting segmented heating technology, in the early stage of glass heating, the temperature is rapidly increased with high power. When approaching the hot bending temperature, the power is reduced to maintain a stable temperature and avoid energy waste caused by excessive heating. In addition, optimizing the placement and spacing of the glass ensures that the heat from the heating tube is evenly transferred to each piece of glass, improving heat utilization efficiency and enhancing production efficiency.
3、 Application of Intelligent Control System
The introduction of an intelligent control system can achieve accurate regulation of the heating tube. Real time monitoring of glass temperature and working status of heating tube using sensors, and automatic adjustment of heating tube power based on feedback information. When the glass temperature approaches the set value, the system automatically reduces the power of the heating tube to avoid increased energy consumption and glass quality issues caused by high temperature. At the same time, through an intelligent scheduling system, production batches are arranged reasonably according to order requirements, reducing equipment idle time, improving equipment utilization, and reducing energy consumption per unit product.
4、 Waste heat recovery and utilization
In large-scale production, if the large amount of waste heat generated by the heating tube is directly discharged, it will cause energy waste. A waste heat recovery device can be installed to use the waste heat for preheating glass or other auxiliary processes. For example, by using a heat exchanger to transfer waste heat to the glass that is about to enter the hot bending process, it can have a certain temperature at the initial stage, reduce the energy consumption required for subsequent heating, and improve production efficiency, achieving a cascade utilization of energy.
In summary, in the large-scale production of 3D hot bending glass, comprehensive measures such as equipment selection upgrade, process optimization, intelligent control, and waste heat recovery and utilization can effectively achieve an optimized balance between heating tube energy consumption and production efficiency, helping enterprises achieve sustainable development in the fierce market competition.