In 3D hot bending glass production, abnormal heating of the heating tube (more than 10% above the set value) may lead to glass deformation, explosion or equipment damage. Perform the following operations: Power off safety Check → System Parameter diagnosis → Hardware fault location.
First, safety power off and appearance of the initial inspection
When abnormal temperature rise is found, immediately press the emergency stop button of the device, cut off the total power supply and wait for the heat pipe to cool naturally (about 30 minutes). Use an infrared thermometer to detect the surface temperature and confirm that there is no high temperature risk. Observe the appearance of the heating tube:
Check whether the wall of the tube has local discoloration, bulging or cracks. If the quartz tube appears white, the material may be deteriorated due to long-term overtemperature;
Check whether the wiring terminals are blackened and carbonized. If there are burn marks, check the line contact resistance (normal value: < 0.1Ω).
Second, temperature control system parameter diagnosis
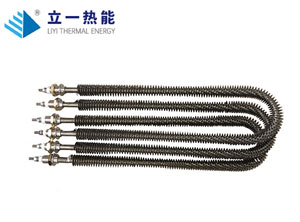
Controller data check:
Enter the temperature controller operation interface and compare the set temperature with the actual feedback value. If the display value fluctuates more than ±5 ° C, calibrate the thermocouple or platinum resistance sensor (error range ±1 ° C);
Check whether the PID parameter is incorrectly modified, and check the proportional gain (Kp) and integral time (Ti). If the deviation of the default value exceeds 20%, the temperature control may be inaccurate.
Temperature control module test:
Use a multimeter to measure the output voltage of the thermostat. When the temperature is set, the output should be adjusted linearly with the temperature change (such as 0-10V analog signal);
If the output is abnormal, short-circuit the signal end of the temperature controller, observe whether the heating pipe continues to heat up, and preliminarily determine whether the module is faulty.
Third, circuit and power anomaly detection
Line check:
Check the power cables in sections, and check the fuses (if the fuse is blown, replace the fast fuse of the same specifications) and the contacts of the AC contactors (if the contact resistance is greater than 0.5Ω, replace the contacts).
Check whether the solid-state relay (SSR) is broken down by measuring the input/output resistance (input > 10kΩ under normal conditions, output infinity).
Power imbalance analysis:
When using a clamp ammeter to measure the three-phase current, if the single-channel current deviation exceeds 15%, there may be local short circuit of the generator tube or uneven power distribution.
For parallel heat pipe sets, the fault individual can be confirmed by breaking a single root test (the current of a single tube should conform to the calculated value of rated power/voltage during normal operation).
4. Check mechanical and environmental factors
Heat dissipation condition check:
Clean the dust on the surface of the heating pipe and the blockage of the equipment air duct, and ensure that the wind pressure of the forced air cooling system is ≥50Pa (can be measured by the wind pressure meter);
Check the circulating water flow rate (≥1.5m/s) and water quality conductivity (< 20μS/cm) of the water-cooled heat pipe. Scale deposition may cause local overheating.
Mechanical interference detection:
Check whether the support of the heating tube is loose. If the vibration causes the tube body to contact the metal parts, local short circuit may be caused.
For rotary hot bending equipment, ensure that there is no risk of collision between the heating tube and the glass movement track to avoid friction heat generation.